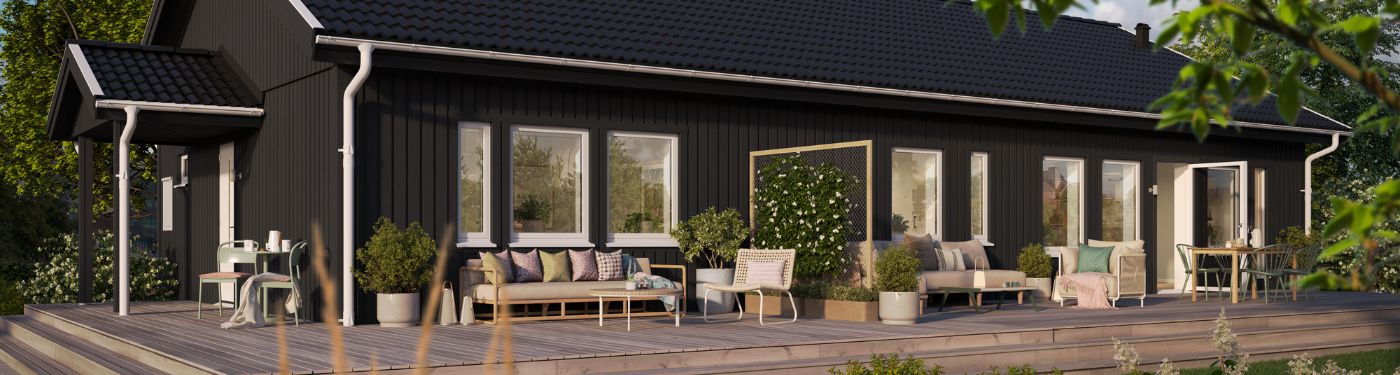
Älvsbyhus
About Älvsbyhus AB
For over 60 years, the family-owned company Älvsbyhus has been building houses all over Sweden. The company offers affordable, prefabricated houses that are delivered turnkey to the plot – always at a fixed price. With its own sawmill and railway tracks, the company maintains a high level of cost efficiency. Today, Älvsbyhus has grown into a Nordic group with operations in Sweden, Finland and Norway. Älvsbyhus builds quality houses at the lowest price on the market, a business concept coined by founders Gunnar and Göran Johansson. Three generations later, the family business is being run by grandsons Kent and Stefan Johansson.
-
Head Office
: Älvsbyn
-
Chairman
: Erik Andersson
Significant events 2024
Celebrates 80 years as a company
Built an entire house indoors at Stockholmsmässan exhibition center
Historically low levels of singlefamily house construction in all three markets
"Where new ways of working are concerned, we tend to let others lead the way through the deep snow and track where they’re heading, and then we follow. We’re not the first, but we’re not the last either”
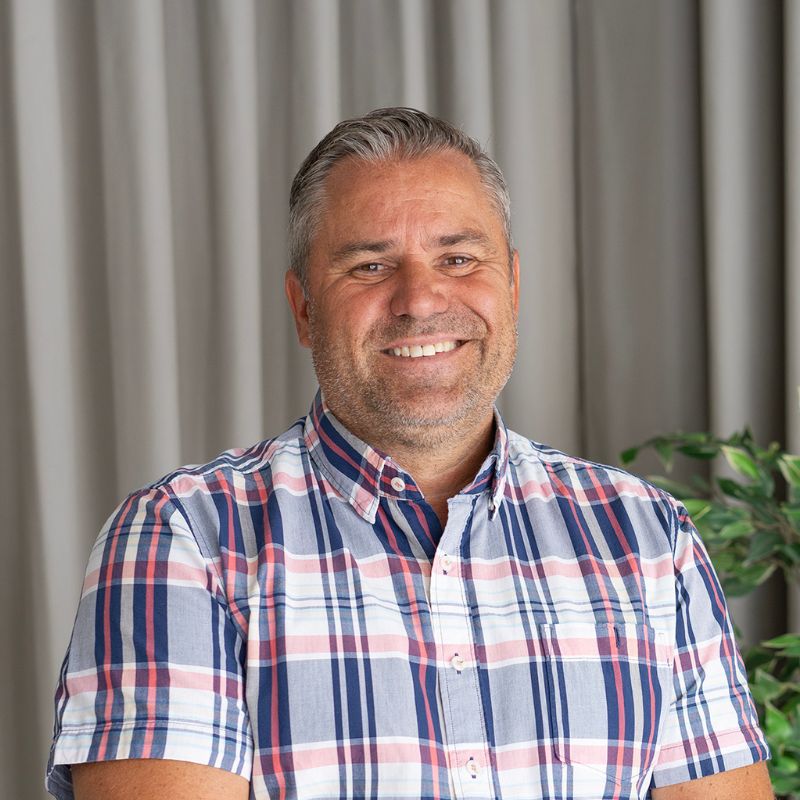
Kent Johansson
CEO, Älvsbyhus
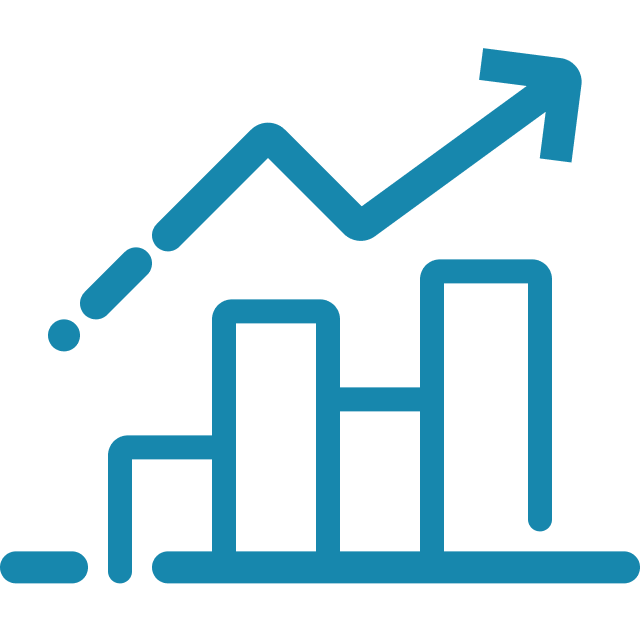
SEK 760 M
Net Sales
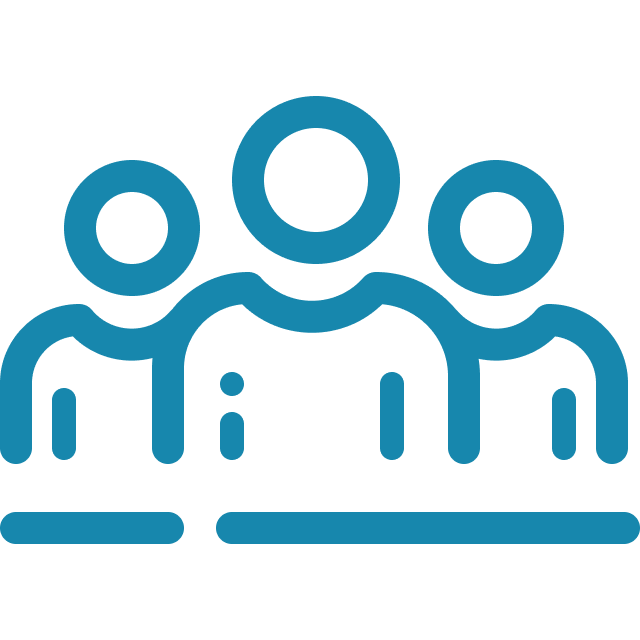
186
Employees
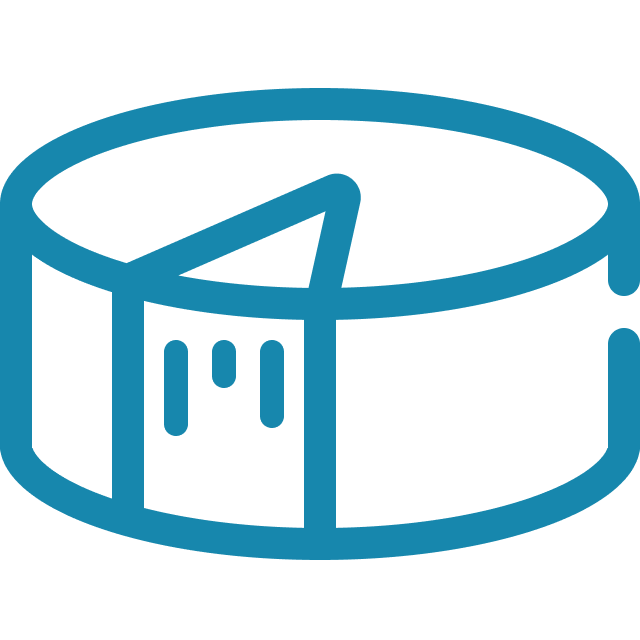
50%
Share
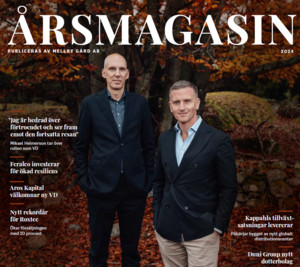